
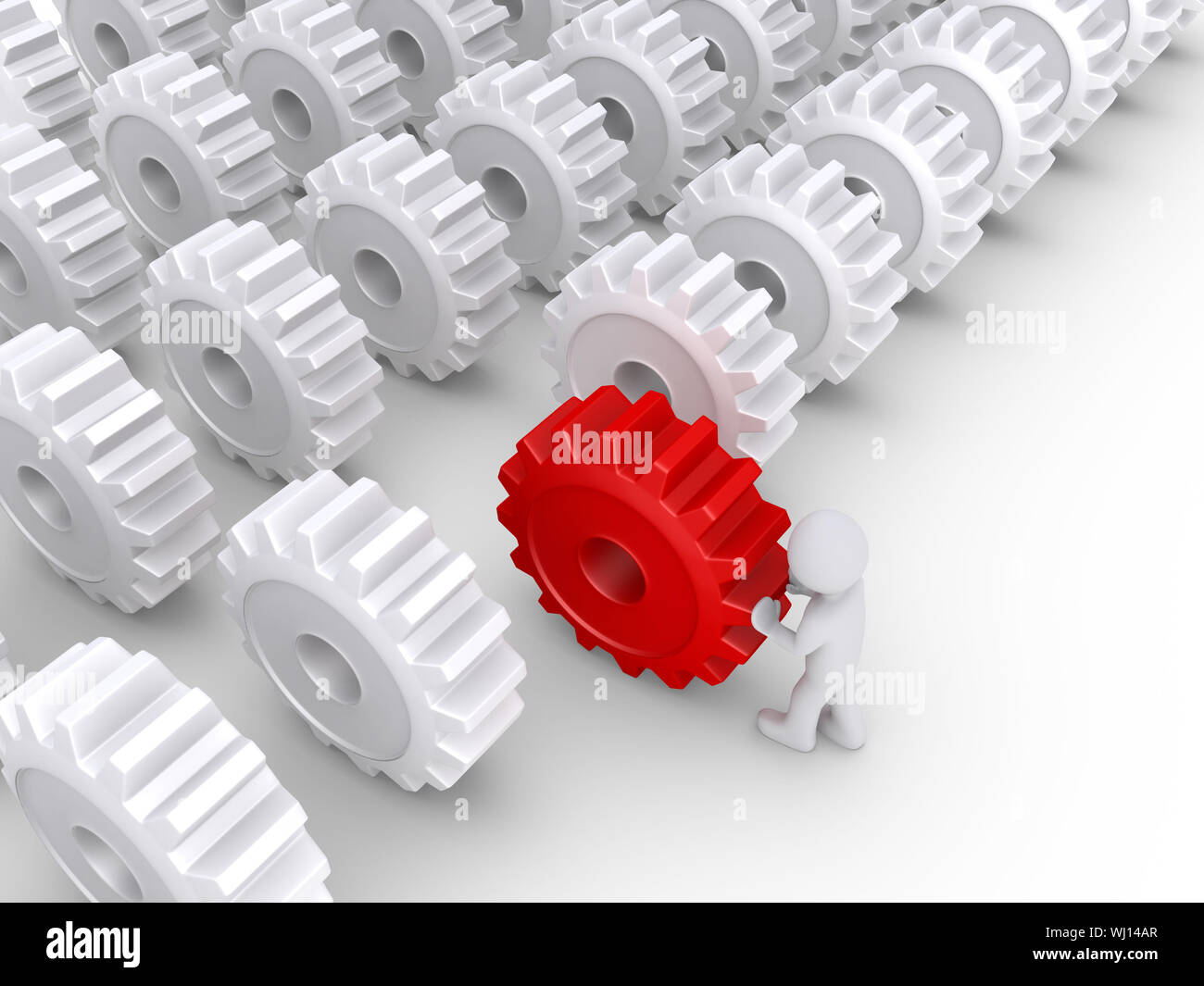
Luckily for middlemen and redistributors, COGS is much more simple to determine. This means the manufacturer’s total number of backpacks sold during this month cost $1,200,000 to produce. Cost of Goods Sold = Beginning Inventory + Purchased Inventory - Ending Inventory.Now, plug them into the cost of goods sold formula: So, let’s identify the variables in this situation: $50,000 on the hourly wages of the warehouse workers responsible for producing the products.Īt the end of the month, the company has a remaining inventory of backpacks that cost $500,000 to make.$50,000 on the plastic for securing the straps.$400,000 on the cloth for the backpacks.Throughout the time period, the company produces an additional batch of backpack making materials at a cost of $700,000, broken down as follows: Let’s say it’s a one-month period and on the first day of the month the company has a beginning inventory of backpacks that cost $1,000,000 to manufacture from material and labor. In that example, calculating cost of goods sold for your backpacks is first done by calculating the total amount of inventory in your possession at the start of the time frame. The metal for zippers, the cloth, the plastic for securing the straps, and even the labor hours directly traceable to production (like hourly wages for warehouse workers) all play a role in the backpack’s production cost.

Product manufacturers have a more complex approach to calculating COGS because of all the components in their inventory.įor example, if you’re manufacturing backpacks, think of everything that goes into making one.
#Cogs business download
Download this Calculator for FreeĬost of Goods Sold Formula for Manufacturers

We’ll go through both to make things clear. Cost of Goods Sold FormulaĬalculating cost of goods sold varies based on if you are the manufacturer or the middleman. We’ll highlight a few tips for that later on in the post. What you want to do is reduce COGS by lowering how much you spend on your inventory. If it’s the latter, you’ve earned no profit. After all, if your cost of goods sold is zero, that either means you’ve acquired your inventory for no cost whatsoever or you sold nothing. To ensure clarity, businesses should look at their COGS for a specific time period (a day, a quarter, a year, etc.) and compare it to a different time period of the same length to see how sales changed.Ī common disclaimer is that COGS is best when it’s low. For example, if your COGS is the same as or lower than your revenue for that time period, it means you’ve broken even or have lost money and are not profitable.
#Cogs business free
You can easily calculate cost of goods sold with our free business metrics calculator.īecause COGS tells business owners how much it costs to acquire what’s to be sold, the number ties directly back to profit and revenue. The formula for calculating cost of goods is: Cost of Goods Sold = Beginning Inventory + Purchased Inventory - Ending Inventory The formula looks at all costs directly traceable to whatever it is you are selling, which is the product and - if you are the manufacturer - the direct labor put into producing the good.
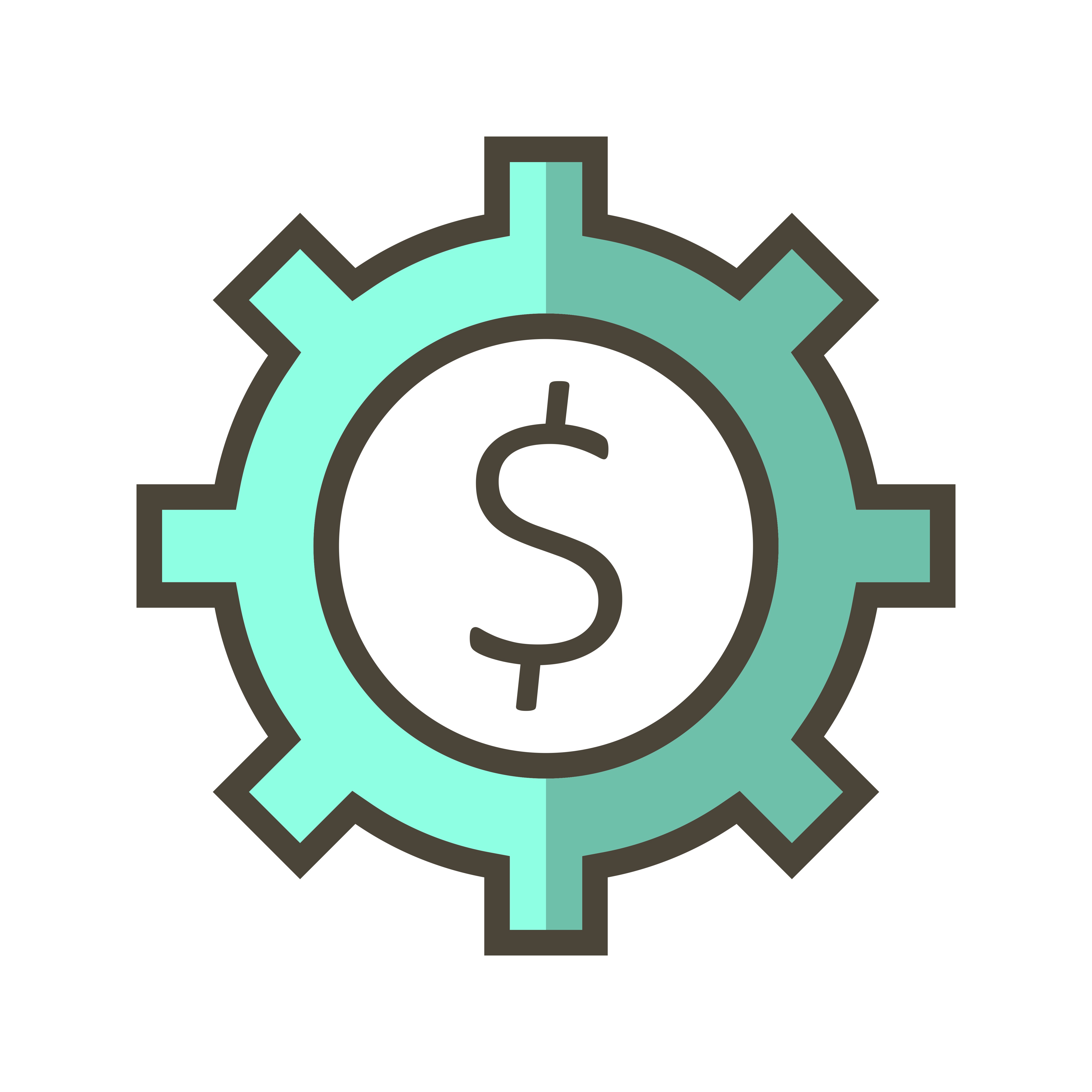
In this blog post, we’ll dive more into what cost of goods sold is and why it matters, go over the cost of goods sold formula, and give you a few tips for optimizing cost of goods sold in your business.Ĭost of goods sold, or COGS, is a business and sales metric that determines the value of inventory sold (and created, if you’re the manufacturer) in a specific time period. Why? Put simply, it’s one of the biggest indicators of revenue, profit, and business sustainability. Any business that sells products needs to know its cost of goods sold.
